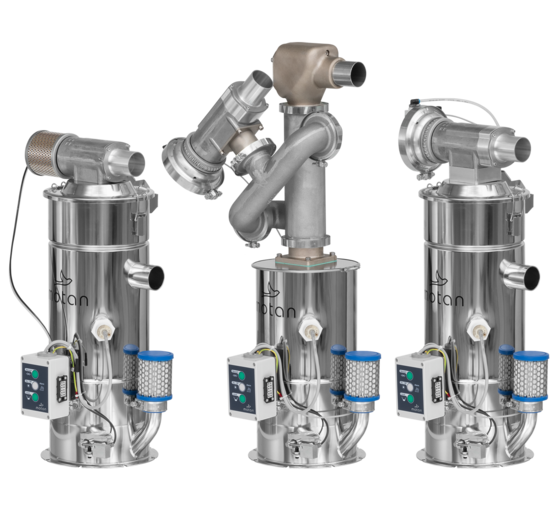
METRO G med
METRO G med material loaders have been specially developed to meet the needs of plastics processors in the medical and pharmaceutical industries and comply with all the strict hygiene requirements according to FDA 21 CFR regulations.
The top priority in the design of the material loaders was the high surface quality of the electro-polished stainless-steel body, ease of cleaning and process reliability. Therefore, strong stainless-steel material sieves, special filters with high quality seals are used which are suitable for clean room applications.
The plastic granulate is conveyed hygienically and without the possibility of contamination to its destination and fed to the machine as required. This eliminates material loss through incorrect handling and keeps the clean room clean and safe. The high-quality hygienic design and technical know-how ensure accurate and reliable operation.
- ×
Granules
METRO G med
Extensive family of material loaders
Suitable for any application.The extensive family of material loaders allows for an optimal selection for any required material throughput. The units are available in 0.5, 1, 3, 6 and 30 liter volumes. In addition to these different unit sizes, different vacuum valve combinations enable an individual solution tailored to your needs.
Granules
METRO G med
Machine loader version
Perfect for hygroscopic materials, space constraints and low throughputs.A machine loader version is available for conveying hygroscopic materials with small throughputs or when space is limited. The discharge module of the device has no discharge flap and is mounted directly on the feed throat of the processing machine.
The advantage is that you do not need a machine hopper and can work with a small supply of material. This is especially important for dried materials and the material dwell time is reduced to a minimum.
Granules
METRO G med
Electropolished stainless-steel
Contamination-free and easy to clean.All material loaders bodies are designed to be as smooth as possible and are made of stainless-steel 1.4301(V2A) and then electropolished. This allows you contamination-free operation and easy cleaning due to the high surface quality.
Granules
METRO G med
Implosion vacuum valve
Ensures constant and stable material delivery and reduces maintenance costs.The strong stainless-steel sieve is automatically cleaned by implosion after each conveying. This guarantees constant and reliable material conveying and reduces the maintenance costs for the unit.
Due to the high-quality seals used in the METRO G med, the material loader operates reliably, and the environment remains dust-free. The HEPA H13 implosion filter is supplied as a standard and enables use in the clean room.
Granules
METRO G med
Membrane implosion vacuum valve
Ideal for clean room conditions - guaranteed free of contamination.The membrane implosion vacuum valve offers the same functions as the implosion vacuum valve but works without compressed air. Instead, the vacuum required for the switching process comes from the conveying system, which opens and closes the valve. This valve is therefore ideally suited for use in clean room applications.
Granules
METRO G med
Dedusting unit
Guarantees consistent material quality for critical applications.The dedusting unit removes dust from high performance engineering plastics directly at the hopper loader, sending them to the central dust filter via the air flow. These expensive materials, now dust-free, can be processed without further delay. The HEPA H13 implosion filter installed as standard enables the machine to be used in clean rooms.
Granules
METRO G med
Hygienic design
For the highest requirements of the medical technology and pharmaceutical industry.All surfaces in contact with the product are made of stainless steel or FDA-compliant plastics and thus the METRO G med hopper loader meets all requirements according to FDA 21 CFR.
- Surfaces that come into contact with granulate have a maximum roughness of 0.8 μm Ra
- Optimal cleanability: no dust corners, rounded transitions, completely removable discharge flap
- Filtered ventilation air (FDA-compliant HEPA H13 air filter)
- Detailed documentation of all components used in the construction of the material loader
Granules
METRO G med
Material inlet flap
Optimum conveying capacity and minimum wear.The material loader inlet flaps make sure that multiple loaders can work together properly in a system. They limit the amount of vacuum required for a group of loaders connected to a coupling station. Thus, no check valves need to be installed in the material flow at the coupling station which would result in a reduction of conveying capacity and increased material abrasion.
An additional benefit of the plasma-nitrided inlet flap is that it acts as a deflector plate at the material inlet, protecting the body of the unit from wear.
Granules
METRO G med
Level sensor
Process reliability - no excess or shortage of granules.A level sensor is installed as standard in all material loaders from 3 liters. The sensor ensures an efficient conveying process by conveying the optimum capacity with each conveying cycle.
Granules
METRO G med
Stainless-steel discharge flap
Optimal material flow and high abrasion resistance.The large material outlet with a stainless-steel discharge flap is abrasion-resistant and meets all requirements for applications in the medical and pharmaceutical industries.
The angled design ensures complete emptying of the material loader after each conveying cycle.
Granules
METRO G med
Discharge flap with spring damper
Prevents material jamming and vacuum loss.A discharge flap with spring damper prevents the flap from completely closing when it is not under vacuum. If there are granulate on the discharge flap at the beginning of pneumatic conveying, these are first sucked away. With increasing vacuum, the flap is then pressed against the spring and will close completely.
Granules
METRO G med
Discharge flap with counterweight
Visual status of the conveying cycle and easy service work.The counterweight of the discharge flap is mounted on the outside so that the current status of the conveying cycle is visible at all times. Due to the easy accessibility, service work can be carried out uncomplicatedly and quickly.
Granules
METRO G med
Loader lid with safety interlock
Safe & easy cleaningAll METRO G med material loaders have a lid with a safety interlock that secures it in the open position. This allows to clean the unit easily and safely.
Granules
METRO G med
Material loader control box
Versatile and easy to use.All METRO G med material loaders are equipped with the C control box. This is our most advanced control box with alarm and status display, on / off button and other functions directly on the unit.
Granules
METRO G med
Material conveying controls
Innovative state-of-the-art controls.METROnet AE and AN is the ultimate networkable system toolkit for complex material conveying systems with either a soft PLC or an S7 PLC with WEBpanel and decentralized CAN bus nodes for connecting peripherals.
All METROnet controllers are fully integrated into the CONTROLnet platform and can be connected to other controllers via Ethernet.